Pipe Schedule and Size Reference Chart:
What is pipe and piping network?
A pipe is a hollow cylindrical conduit that can be constructed from materials such as metal, plastic, wood, concrete, or fiberglass. It serves to transport fluids, gases, slurries, or fine particles. A piping system encompasses not only the network of interconnected pipes but also includes in-line components like pipe fittings and flanges. Additionally, equipment such as pumps, heat exchangers, valves, and tanks are integral to the overall piping system. Piping systems are crucial to industrial operations, acting as the lifeblood of various processes.
The initial design of a piping system is driven by the functional need to convey fluids from one location to another. Detailed design considerations involve factors such as the type of fluid being transported, allowable pressure drops or energy losses, desired flow velocity, spatial constraints, and specific process requirements like free draining or straight runs. Other factors include stress analysis and the temperature of the fluid.
Supporting a piping system involves significant engineering and design efforts, as well as fabrication and installation. In certain instances, specialized support structures (such as structural T’s, inverted L’s, cantilevers, U-portals, and pedestals) must be constructed exclusively to provide adequate support for the piping network.
What is pipe schedule?
Pipe Schedule is a standardized system used to denote the wall thickness of steel pipes, expressed as a numerical index rather than a direct measurement. This index is derived from a specific calculation that correlates with both the pipe’s nominal pipe size (NPS) and wall thickness.
Pipes with the same nominal diameter may have different schedules, which correspond to variations in wall thickness. For applications requiring higher pressure or enhanced structural integrity, a higher schedule number is chosen, signifying a thicker pipe wall.
In stainless steel piping, the schedule number is often followed by the letter “S,” indicating the material’s enhanced strength characteristics. This enables stainless steel pipes with thinner walls to withstand the same pressure as thicker-walled carbon steel pipes.
The manufacturing process, especially for larger diameters, can impact pipe dimensions and introduce additional considerations when selecting pipes for applications.
Standards followed:
Pipe schedules are standardized to ensure uniformity in pipe dimensions and performance across industries, with various organizations regulating these standards. ASME B36.10M and ASME B36.19M govern dimensions for carbon and alloy steel, as well as stainless steel pipes, respectively, while ANSI/ASME B31.3 focuses on process piping. The API standards, such as API 5L for steel line pipes in the petroleum and natural gas industries, and API 5B for threading and inspection of casing and tubing, are also critical. Internationally, ISO 4200 covers plain-end steel tubes, and ISO 1127 sets standards for stainless steel tubes.
German standards like DIN 2448 for seamless steel pipes and DIN EN 10220 for welded tubes are also widely used, along with JIS standards like JIS G3454 for carbon steel pipes and JIS G3459 for stainless steel pressure pipes. ASTM A53, ASTM A312, and ASTM A106 define standards for welded, seamless, and high-temperature service pipes. The MSS-SP series includes standards for fittings, valves, and flanges that ensure compatibility within piping systems. Common pipe schedules include 5, 10, 20, 40, 80, 160, STD (Standard), XS (Extra Strong), and XXS (Double Extra Strong), with the pipe schedule number calculated based on nominal size and pressure rating. These standards are crucial for applications in industries such as oil and gas, chemical processing, and power generation, ensuring safety, durability, and performance across diverse conditions.
Importance and Operational Methodology:
Piping systems are integral to industrial processes, acting as the primary conduits for the conveyance of fluids, gases, and slurries across sectors such as oil and gas, petrochemical, and manufacturing. Their design, fabrication, and installation are crucial to ensuring operational safety, optimizing system efficiency, and maintaining the structural reliability of industrial equipment. The precise selection of pipe schedules, materials, and associated components is vital to meet operational demands, such as handling pressure, temperature gradients, and flow rates, while reducing energy losses and preserving mechanical integrity under varying conditions.
Define Process Parameters:
Evaluate critical process variables such as fluid type, pressure rating, operating temperature, and flow velocity. These parameters dictate the choice of pipe material, nominal pipe size (NPS), and associated design specifications.
Pipe Schedule Selection:
Choose the appropriate pipe schedule based on pressure class and pipe diameter, in accordance with industry standards such as ASME, API, or ASTM, ensuring the pipe wall thickness meets both structural and process requirements.
Material and Component Selection:
Identify appropriate piping materials (e.g., carbon steel, stainless steel) and auxiliary components like fittings, flanges, and valves. These must be compatible with both the service environment and fluid characteristics (e.g., corrosion resistance, temperature tolerance).
Design of Pipe Support Systems:
: Engineer suitable support configurations, accounting for pipe weight, thermal expansion, and dynamic loads. Utilize specific support structures, such as hangers, anchors, and specialized frameworks (e.g., pedestals, cantilevers) to maintain system stability and prevent mechanical deformation.
Execute Stress Analysis:
Conduct detailed stress analysis, considering thermal expansion, vibration, and external forces that could impact system performance. This analysis ensures that the piping system can withstand mechanical loads without compromising structural integrity. By adhering to these methodologies, mechanical engineers can effectively design and implement piping systems that fulfil industrial process requirements, while adhering to rigorous safety standards and minimizing the potential for system failure or operational disruptions.
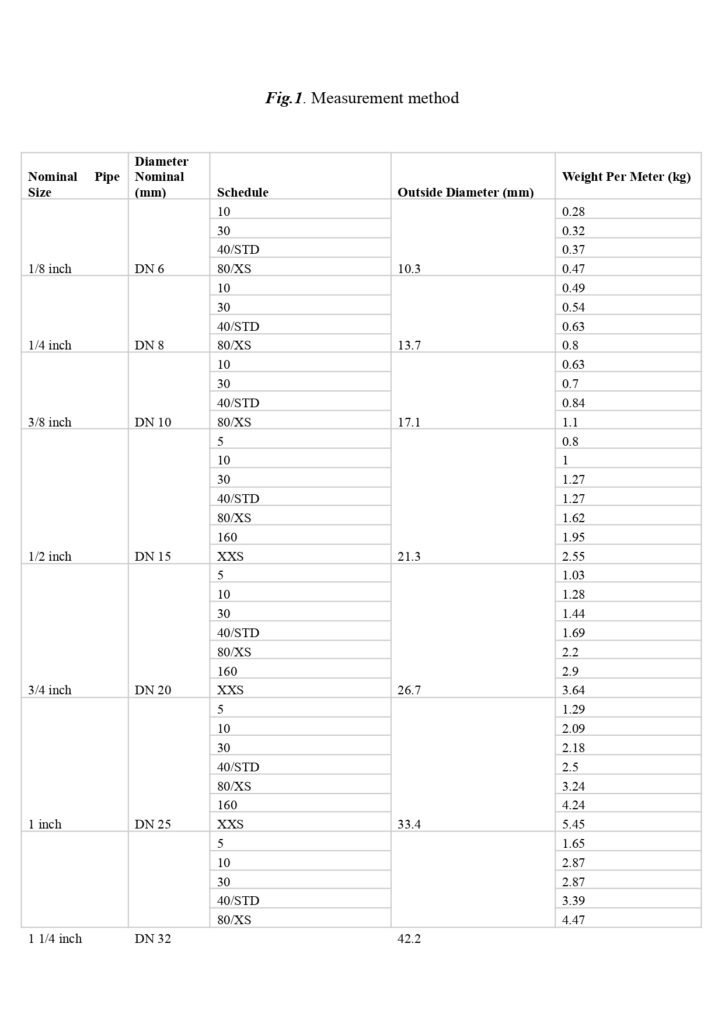

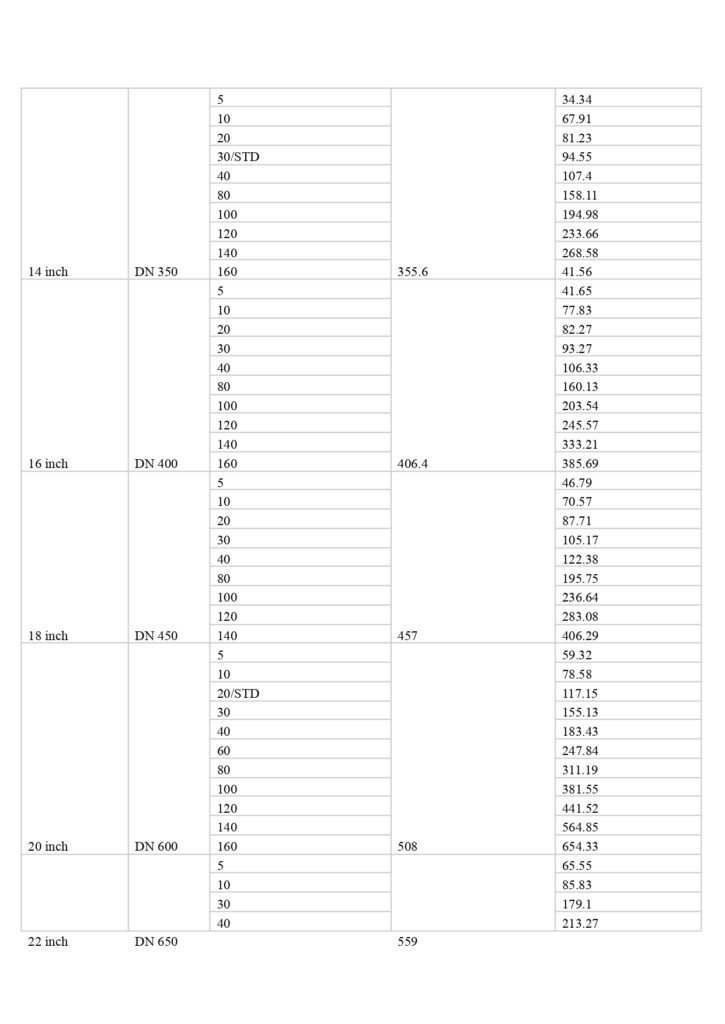
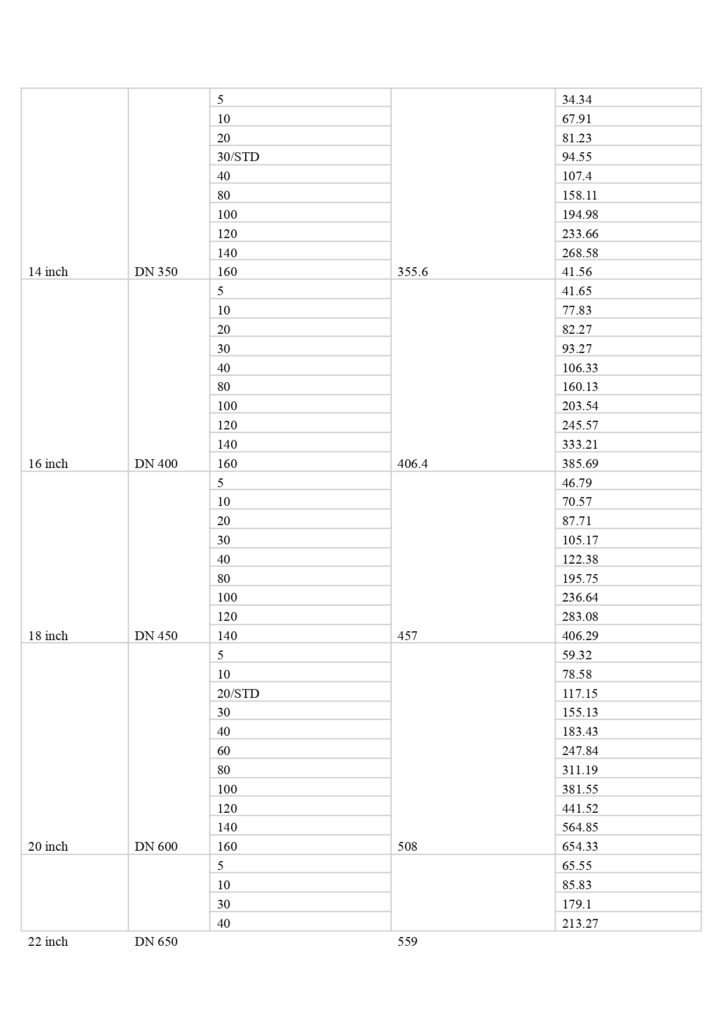
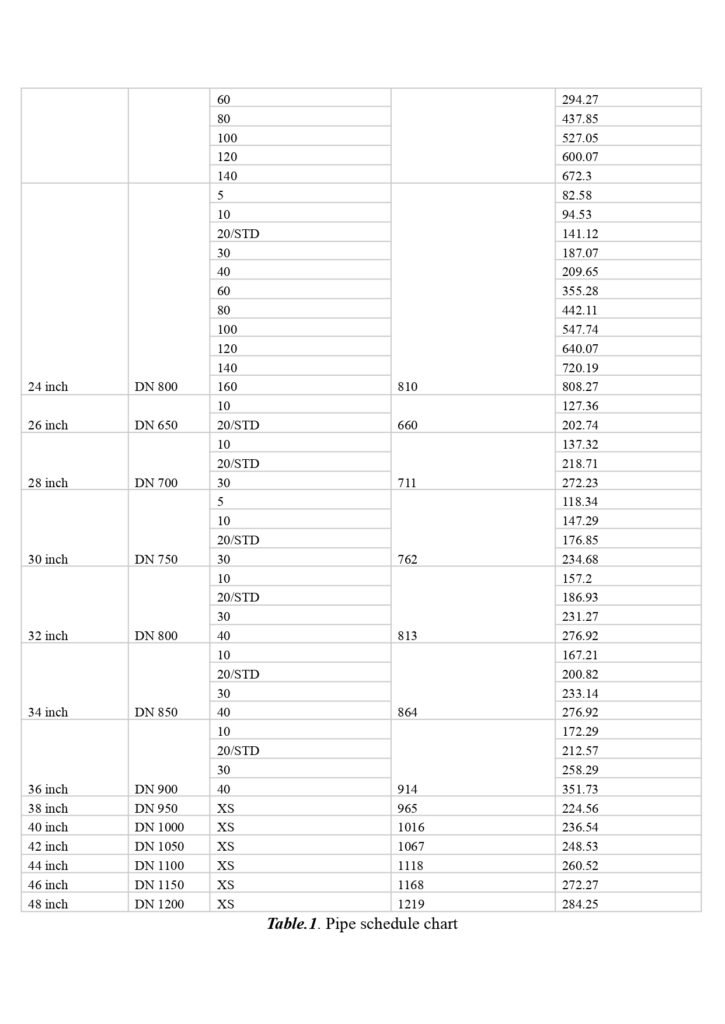